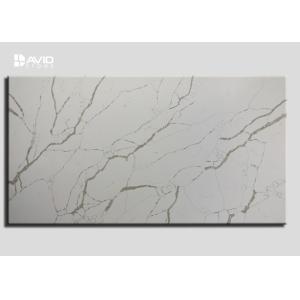
Add to Cart
White Calacatta Quartz Stone Slab 1.6x3.2m ideal for Quartz Countertop
Our Calacatta quartz stone slab are made from specially selected raw materials having a combination of clear transparent Rock Crystal like appearance and white quartz texturing within the stones. The natural patterns & texture within the semiprecious stones impart a unique look to the interiors – white in colour, very natural & subtly luxurious
Quartz stone molding process:
The synthesis of quartzite is mainly controlled by a computer in a vacuum die-casting machine. The process is mostly cured by medium temperature.
In accordance with the needs of the proportion of different filler mixed mesh, and has good temperature caused by resin and colorant mixture, and the pumping to the upper part of the hopper pouring machine, mixing. In the pouring mouth, ready to die with the console to control the moving speed and direction of the sprue and the feeding speed of pouring, pouring is completed, will be sent to the following mold press, by vacuum pressure pressing, and then treated by high temperature, finally finished polishing.
1, Selection and mixing of raw materials
Looking for high quality quartz mineral and other additives, a variety of quartz mineral raw grain size to purify by special cleaning equipment, removal may contain impurities such as wood, metal pieces, and then delivered to the raw material mixing tower, step by step will evenly mixed minerals and other additives were.
The raw material and uniform mixing without impurity are the fundamental guarantee of the sheet defect.
2, Thickness shaping
Mix and mix the raw materials into the super large molding machine. The thickness and thickness of the sheet material can be adjusted accurately by the computerized induction thickening equipment. After molding, it is directly placed on the belt conveyor, forming only one sheet at a time.
3. Vacuum die-casting
Molding blank in vacuum die casting machine by computer precise control of the whole process, vacuum equipment is installed on the bottom of the mineral space within the air to close the vacuum, forming the most closely packed ore, mineral powder and other additives, achieve no hole effect, operation time of each sheet in about 15 minutes.
The vacuum die-casting of each sheet of super large size is used to ensure the density and no hole of the material. The greater the size of the sheet, the more complex the process is.
4. The plate from the vacuum die-casting machine is sent directly into the drying building at 90-110 C, and the medium temperature is cured 50-120min. The baking building for a period of time is that the quartz stone plate has reached a certain degree of curing. To ensure the excellent properties of the plate.
5, surface polishing
On the automatic roller conveyor line, the plate is moved slowly, and the surface is polished to form a special glossy mirror effect through 36 coarse and fine large special grinding heads rotating at high speed and moving at uniform speed, supplemented by a large number of cooling water and different abrasives.
Testing data of our quartz stone slab
Density | 2350kg/m3 |
Moh’s hardness (polished): | 6-8 |
Abrasion resistance(polished) | 51 |
Specular Gloss (60℃) | 42.5 |
Absorption by weight | <0.05% |
Flexural strength | Dry condition: 35.8Mpa; Wet condition: 38.0Mpa |
Compressive strength: | Dry condition: 199Mpa; Wet condition: 192Mpa |
Abrasion resistance of unglazed tiles (polished) | 39mm3 |
Linear thermal expansion coefficient | 35x10-6/℃ |
Radioactivity | Class A |
Some details:
Quartz stone slab packing: